One of the most prominent hurdles in operating manufacturing plants is to regulate the enervating heat produced by industrial processes. Therefore, an efficient industrial cooling system is the fulcrum of managing a profitable, sustainable, and robust industrial facility. There are various cooling system designs and structures to provide versatile heat regulation for different business requirements. For instance, natural draft cooling benefits the density discrepancy between the produced hot air and ambient fresh air, mechanical draft cooling utilizes sprayed hot water to transfer heat from a condenser to dry air, and water cooling uses cold water directly to reduce the targeted component temperature.
Ā
When all cooling requirements are considered, water cooling options are still the most popular and budget-friendly cooling systems applicable to various cooling scenarios, including but not limited to condominiums, office buildings, and industrial facilities. Water cooling systems, also known as hydronic cooling systems, are mainly considered as the most adaptable and advantageous HVAC (heating, ventilation, and air conditioning) systems utilizing water to transfer heat from one location to another[1]. Since hydronic HVAC systems use water to absorb and transfer heat, they are more energy efficient as compared to air-based systems since water has a higher thermal capacity. According to the applied heat transfer method and water source, water-based cooling systems provide design flexibility with low-maintenance.
Ā
Nonetheless, despite the advantages of relying on water as a coolant, water-based HVAC systems still require regular inspection and maintenance to retain peak condition and avert pernicious cooling aberrations deteriorating heat regulation for industrial facilities, office buildings, or houses. Since water-based cooling equipment is a part of various demanding industrial applications[2], including but not limited to chemicals or petrochemicals, welding, medical, pharmaceutical, automotive, data centers, and metalworking, maintaining consistent and reliable heat transfer is essential to sustain profitable business growth. Thus, to reduce production costs and increase manufacturing efficiency, mechanics should examine each cooling component painstakingly and regularly.
Ā
Since hydronic HVAC systems can be intricate and multifaceted depending on the application requirements, there are plentiful malfunctions that can affect cooling efficiency and heat transfer capacity, resulting in catastrophic production downtime for industrial processes. For instance, chillers using metal tubes (copper or carbon steel) to circulate water are susceptible to corrosion and abrasion, leading to leaks and component failures. Accumulating sediment or particulates in the complex tubing systems can corrode or clog pipes, leading to inadequate heat transfer. Or, perforce, neglected electronic components can degrade and fail due to prolonged wear and tear, leading to inconsistent cooling results. Unfortunately, these HVAC system malfunctions not only deteriorate industrial process sustainability but also engender hazardous environmental impacts due to high energy loss.
Ā
Water-based or not, an installed HVAC system accounts for up to 50% of the total energy consumption of an establishment, surpassing the total energy consumption of lighting, elevators, and office equipment[3]. Thus, an unnoticed abnormality can multiply energy consumption while the HVAC system tries to compensate for the heat transfer loss. Furthermore, since HVAC systems are tightly coupled systems and operate with protracted lag and inertia, they are vulnerable even to minuscule abnormalities due to the ripple effect of a single equipment failure, whether a capacitor, pipe, or gasket.
Ā
Relevant data indicates that the amount of energy waste caused by a malfunctioning cooling system and faulty control accounts for about 15%ā30% of the total energy consumption of studied facilities. Thus, by running a malfunctioning cooling system, buildings became profligate energy devourers, resulting in harsh energy production demands causing excess carbon and methane emitted into the atmosphere. Therefore, applying real-time (automated) malfunction diagnosis to HVAC systems can abate excessive energy consumption and improve energy efficiency leading to savings ranging from 5% to 30% [3]. In addition to preventing energy loss, automated HVAC fault detection can extend equipment lifespan, avoid profit loss, and provide stable heat transfer during industrial processes. In that regard, automated malfunction detection also obviates exorbitant overhaul processes due to prolonged negligence, leading to a nosedive in production quality.
Ā
After perusing recent research papers on detecting component failures to automate HVAC maintenance, I noticed that there are no practical applications focusing on identifying component abnormalities of intricate water-based HVAC systems to diagnose consecutive thermal cooling malfunctions before instigating hazardous effects on both production quality and the environment. Hence, I decided to build a versatile multi-model AIoT device to detect anomalous sound emanating from cooling fans via a neural network model and to diagnose consecutive thermal cooling malfunctions based on specifically produced thermal images via a visual anomaly detection model. In addition to AI-driven features, I decided to develop a capable and feature-rich web application (dashboard) to improve user experience and make data transfer easier between development boards.
Ā
As I started to work on developing my AI-powered device features, I realized that no available open-source data sets were fulfilling the purpose of multi-model HVAC malfunction diagnosis. Thus, since I did not have the resources to collect data from an industrial-level HVAC system, I decided to build a simplified HVAC system simulating the required component failures for data collection and in-field model testing. I got heavily inspired by PC (computer) water cooling systems while designing my simplified HVAC system. Similar to a closed-loop PC water cooling design, I built my system by utilizing a water pump, plastic tubings, an aluminum radiator, and aluminum blocks. As for the coolant reservoir, I decided to design a custom one and print the parts with my 3D printer. Nonetheless, since I decided to produce a precise thermal image by scanning cooling components, I still needed an additional mechanism to move a thermal camera on the targeted components ā aluminum blocks. Thus, I decided to design a fully 3D-printable CNC router with the thermal camera container head to position the thermal camera, providing an automatic homing sequence. My custom CNC router is controlled by Arduino Nano and consists of a 28BYJ-48 stepper motor, GT2 pulleys, a timing belt, and gear clamps. While producing thermal images and running the visual anomaly detection model, I simply added an aquarium heater to the closed-water loop in order to instantiate aluminum block cooling malfunctions.
Ā
As mentioned earlier, to provide full-fledged AIoT features with seamless integration and simplify complex data transfer procedures between development boards while constructing separate data sets and running multiple models, I decided to develop a versatile web application (dashboard) from scratch. To briefly summarize, the web dashboard can receive audio buffers via HTTP POST requests, save audio samples by given classes, communicate with the Particle Cloud to obtain variables or make Particle boards register them, produce thermal images from thermal imaging buffers to store image samples, and run the visual anomaly detection model on the generated thermal images. In the following tutorial, you can inspect all web dashboard features in detail.
Ā
Since this is a multi-model AI-oriented project, I needed to construct two different data sets and train two separate machine learning models in order to build a capable device. First, I focused on constructing a valid audio data set for detecting anomalous sound originating from cooling fans. Since XIAO ESP32C6 is a compact and high-performance IoT development board providing 512KB SRAM and 4 MB Flash, I decided to utilize XIAO ESP32C6 to collect audio samples and run my neural network model for anomalous sound detection. To generate fast and accurate audio samples (buffers), I decided to use a Fermion I2S MEMS microphone. Also, I connected an SSD1306 OLED display and four control buttons to program a feature-rich on-device user interface. After collecting an audio sample, XIAO ESP32C6 transfers it to the web dashboard for data collection. As mentioned earlier, I designed my custom CNC router based on Arduino Nano due to its operating voltage. To provide seamless device operations, XIAO ESP32C6 communicates with Arduino Nano to move the thermal camera container head.
Ā
After completing constructing my audio data set, I built my neural network model (Audio MFE) with Edge Impulse to detect sound-based cooling fan abnormalities. Audio MFE models employ a non-linear scale in the frequency domain, called Mel-scale, and perform well on audio data, mostly for non-voice recognition. Since Edge Impulse is nearly compatible with all microcontrollers and development boards, I have not encountered any issues while uploading and running my Audio MFE model on XIAO ESP32C6. As labels, I simply differentiated the collected audio samples by the cooling fan failure presence:
Ā
Ā
normal
Ā
Ā
defectiveĀ
Ā
Ā
After training and testing my neural network model (Audio MFE), I deployed the model as an Arduino library and uploaded it to XIAO ESP32C6. Therefore, the device is capable of detecting anomalous sound emanating from the cooling fans by running the neural network model onboard without any additional procedures or latency.
Ā
Since I wanted to employ the secure and reliable Particle Cloud as a proxy to transfer thermal imaging (scan) buffers to the web dashboard, I decided to utilize Photon 2, which is a feature-packed IoT development board optimized for cloud prototyping. To collect accurate thermal imaging buffers, I employed an MLX90641 thermal imaging camera producing 16x12 IR arrays (buffers) with fully calibrated 110° FOV (field-of-view). Also, I connected an ST7735 TFT display and an analog joystick to program a secondary on-device user interface. Even though I managed to create a snapshot (preview) image from the collected thermal scan buffers, Photon 2 is not suitable for generating thermal images, saving image samples, and running a demanding visual anomaly detection model simultaneously due to memory limitations. Therefore, after registering the collected thermal scan buffers to the Particle Cloud, I utilized the web dashboard to obtain the registered buffers via the Particle Cloud API, produce thermal image samples, and run the visual anomaly detection model.
Ā
Considering the requirements of producing accurate thermal images and running a visual anomaly detection model, I decided to host my web application (dashboard) on a LattePanda Mu (x86 Compute Module). Combined with its Lite Carrier board, LattePanda Mu is a promising single-board computer featuring an Intel N100 quad-core processor with 64 GB onboard storage.
Ā
After completing constructing my thermal image data set, I built my visual anomaly detection model with Edge Impulse to diagnose ensuing thermal cooling malfunctions after applying anomalous sound detection to the water-based HVAC system. Since analyzing cooling anomalies based on thermal images of HVAC system components is a complicated task, I decided to employ an advanced and precise machine learning algorithm based on the GMM anomaly detection algorithm and FOMO. Supported by Edge Impulse Enterprise, FOMO-AD is an exceptional algorithm for detecting unanticipated defects by applying unsupervised learning techniques. Since Edge Impulse is nearly compatible with all microcontrollers and development boards, I have not encountered any issues while uploading and running my FOMO-AD model on LattePanda Mu. As labels, I utilized the default classes required by Edge Impulse to enable the F1 score calculation:
Ā
Ā
no anomalyĀ
Ā
Ā
anomalyĀ
Ā
Ā
After training and testing my FOMO-AD visual anomaly detection model, I deployed the model as a Linux (x86_64) application (.eim) and uploaded it to LattePanda Mu. Thus, the web dashboard is capable of diagnosing thermal cooling anomalies based on the specifically produced thermal images by running the visual anomaly detection model on the server (LattePanda Mu) without any additional procedures, reduced accuracy, or latency.
Ā
In addition to the discussed features, the web dashboard informs the user of the latest system log updates (completed operations) on the home (index) page automatically and sends an SMS to the verified phone number via Twilio so as to notify the user of the latest cooling status.
Ā
Considering the complex structure of this device based on a customized water-based HVAC system, I decided to design two unique PCBs after testing the prototype connections via breadboards. Since I wanted my PCB designs to represent the equilibrium of cooling fan failures and thermal (heat) malfunctions, I got inspired by two ancient rival PokĆ©mon ā Kyogre and Groudon.
Ā
Finally, in addition to the custom CNC router and coolant reservoir parts, I designed a plethora of complementary 3D parts, from unique PCB encasements to radiator mounts, so as to make the device as robust and compact as possible. To print flexible parts handling water pressure, I utilized a color-changing TPU filament.
Ā
So, this is my project in a nutshell š
Ā
Click here to inspect code files, STL files, firmware, assets, and machine learning models.

Ā

Ā

Ā

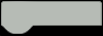