Hi, there! Just got several micro servos (9g180°, 9g300°, 2kg180°, 2Kg 300°). Today I am going to test them, and figure out the differences among them and see where they can be used. Hope this will be helpful for someone who just wants to get a servo like this kind.
Servo Overview


In the first picture, it’s a 9g 180°servo and it comes with several accessories: servo arms of different shapes, round plate, screws, servo damping rubber, etc.
For more information, you also can click the link the go to their web-pages:
There are many kinds of servos on the market, what I got here is called clutch servo, what does that mean? How is it different from other servos?
I picked up several key points for your reference:
First of all, the reason why they are called clutch servo is that these servos have a clutch function.
What is the clutch function aimed for?
When the angle of a servo is changed by external forces during normal operation, the servo can automatically reset and continue working through the clutch function, which prevents it from being damaged. This makes it different from other normal servos.
Electronic Protection
After being blocked for 5 seconds, the servo will automatically turn off its power to avoid getting burned.
What are the differences between these servos I got? Here are details about that:
Internal Structure

These clutch servos are the same in internal structure, but they have different mechanic dimensions, which leads to the differences in size.
9g 180° Clutch Servo

9g300°Clutch Servo

2kg180° Clutch Servo

2kg300° Clutch Servo

Specification

From the technical specification table, the main differences of these clutch servos are the operating angle and stall torque.
The 6kg clutch servo with large torque is suitable for small robots, and the operation angle should be selected according to specific needs. 2kg clutch servo can be used for remote control of vehicle and ship model. The 9g clutch servo is light weight, which is suitable for UAV and other aircraft models.
You can select them according to your needs.
OK, now, I will connect a servo to my Arduino board, and write a simple program to test it.

I used Mega sensor expansion board V2 here. Connect the servo to digital port 14, and install a servo arm on it.
Open Arduino IDE, select the related development board and port.

Write a simple program to let the servo turn 180° and then back to 0° repeatedly. As shown below:

The effect is shown below.
Then let’s check the clutch function of the servo.
From the videos above we can see that, when I stop the servo arm deliberately and then release it, it recovers immediately. Then, I stop the servo and rotate its arm for several circles, it can still back to normal, no block, very fluently.
Conclusion
These micro clutch servos are really convenient to use and easy to install. Compared with common servos, they are equipped with clutch function and electronic protection function. That is, when there is an external force to change the servo angle during normal operation, it can reset automatically and continue to work through clutch function, which makes up for the defect that a common servo is easy to be damaged by an external force during operation. And The electrical protection function greatly enhances the service life of the product.
These servos are lightweight, but also have the characteristics of large torque, stable operation and accurate operation angle.
There is no limit inside the servo, which can rotate 360 degrees (only manual rotation) without block problem. At the same time, the servo power is small so it can work properly with an ordinary battery or USB power supply.
These servos can be controlled by calling the servo library on Arduino IDE, and the maximum rotation angle is about 180 ° in the pulse range of 500-2500 μ sec.
That's all for today's servo test. If you are interested in this product, you can start to dig into its application scenarios.

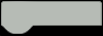