This project describes how to create a simple charger for various types of 1-cell batteries using HVPAK.
Story
The designed charger uses Constant Current Constant Voltage (CCCV) charging control circuit. The application also includes a safety operation timer, undervoltage, overcurrent, and thermal protection.
The HVPAK Battery Charger is a high-efficiency switch-mode battery charger suitable for 1-cell lithium-ion or lithium-polymer applications.
You may download Go Configure™ Software Hub to open the .gp files and view the proposed circuit design. Use the GreenPAK development tools to freeze the design into your own customized IC in a matter of minutes. Also, you may review a complete library of application notes featuring design examples as well as explanations of features and blocks within the IC.
Operating Principle
The Constant Current Constant Voltage battery charging method is a charging process that uses the constant current in the initial stage of charging and then switches to constant voltage in later stages of charging when the battery reaches the set charge level.
Advantages of the CCCV battery charging method include:
1. Fast charging: The use of the direct current in the initial stage of charging allows the battery to be charged quickly, ensuring more efficient use of time.
2. Voltage Control: Once a set charge level is reached, a constant voltage helps avoid overcharging the battery, ensuring a safe charge level.
3. Versatility: The CCCV method can be applied to different types of batteries, such as lithium-ion, nickel-metal hydride, and others, ensuring the versatility of using this method to charge different types of batteries.
4. Charge efficiency: The CCCV method achieves high charge efficiency because the constant current in the initial stage allows for the maximum charge current, and the constant voltage in the later stages helps to ensure a stable charge voltage.
5. Flexibility: The CCCV method can be adapted to different charging requirements depending on the battery type, state of charge, and other factors, allowing more flexibility in setting up the charging process.
This design also has a Pre-Charge Stage. This is the first step in the battery charging process, which is used to reduce the initial charging current when connecting a discharged battery to a power source.
During discharge, the battery loses its electrical potential difference, and the internal resistance can be high. When such a discharged battery is connected to a charger, the high charging current can cause the high voltage across the battery terminals, which can cause arcing and damage to the battery terminals or cells.
Therefore, the Pre-charge stage involves the application of an initially limited charging current that is steadily increased over time to avoid such problems. This allows the battery to be gradually saturated with electrical energy, reducing the impact of high currents on its cells.
The Pre-charge stage is commonly used in some battery chargers, particularly automotive chargers, and chargers for large battery systems. It helps to ensure the safe and efficient charging of the battery, protecting it from possible damage during the initial charging stage.
The Li-ion Battery Charge Profile is shown in Figure 1.

The Operation Flow Chart is shown in Figure 2.

There is also an LED to notify about the process:
LED is OFF — no charging;LED is ON — charging process;LED is blinking — charge termination.
GreenPAK Design
The GreenPAK (HVPAK) Design is presented in Figure 3.
If the VUSB is connected, PIN3 detects it and powers ON the ACMP0H. ACMP0H checks the VDD voltage level, if it is higher than 4.5 V, the output is HIGH and all processes can be started.
Then ACMP1H checks the Vbat voltage. DFF4’s output is HIGH, so no voltage divider is connected to PIN20 (IN+ Source of the ACMP1H). If Vbat is lower than 3 V the Pre-charging stage starts (3-bit LUT8 is a stage selector). PWM0 sets the reference voltage for CCMP0. Thus, CCMP0 and MF2 (3-bit LUT8 and CNT2/DLY2) control the current for the appropriate stage. In this case, the Up/Down input of the PWM0 macrocell is LOW, which means that we start charging from 256 mV for CCMP0 Vref (Figure 4). As a result, the CCMP0 maintains the ~ 97 mA current.
As far as the ACMP1H output is HIGH (the Vbat is higher than 3 V), the DFF4 output goes to LOW and the voltage divider is connected to PIN20. The Constant Current phase starts. In this case, the ACMP0H makes a comparison for 4.2 V (not 3 V as in 1st case). The Up/Down input of the PWM0 is HIGH, so the CCMP0 Vref is 1440 mV. The resulting current is ~ 550 mA. Note that these current limits can be changed by changing the Vref value in the Reg File or by changing the resistor connected to the PIN 5 (Sense A).
This CC phase continues until the battery voltage reaches 4.2 V (ACMP1H output is HIGH). Then the Constant Current stops and the Constant Voltage phase starts. In this case, the ACMP1H controls the constant voltage of 4.2 V and the CCMP1 just checks and keeps the current decreasing and lower than the IBF of 97 mA until the battery is fully charged. When the battery is fully charged, the charging process stops, and all corresponding blocks are in Sleep Mode (CHG_Sleep is High).

In addition, the CNT0/DLY0 sets the 24 h safety operation timer as soon as the Vusb is detected. If the charging is not complete during 24 h, the CHG_Sleep is HIGH and the system is powered down. This time is set by CNT0/DLY0 and can be changed due to the charger settings and battery type.
Note: this design describes how to create a CCCV Battery Charger for 1-cell batteries.
Design Testing
The following figures show the charging process at each stage: Figure 5 — Pre-charge, Figure 6 — Constant Current, Figure 7 — Constant Voltage.
The blue channel represents PIN 7 and PIN 8 output, the red channel — Vbat+, and the green — PIN 5 Sense A.



Conclusion
We've described how to configure the HVPAK to create a simple Charger for various types of 1-cell batteries. The Designed Charger uses the CCCV method. The application also includes a safety operation timer, undervoltage, overcurrent, and thermal protection.
The HVPAK’s internal resources, including the HV, oscillators, logic, and GPIOs are easy to configure to implement the desired functionality for this design.
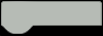