This is an incredibly cheap and visually fascinating toy through which we can learn a lot about the behavior and physics of standing waves.
Ultrasonic levitation is phenomenon where objects are suspended in mid-air using the power of sound waves. Specifically, it involves the use of high-frequency sound waves, typically beyond the range of human hearing (above 20 kHz), to create a standing wave pattern that can counteract the force of gravity and hold small objects in place.

In one of my previous videos, I described a way to make an ultrasonic levitation device, which, although seemingly simple to make, in practice required lengthy setup, used some unusual components, and required a lot of power. I recently came across an Ultrasonic Levitation kit that contains components, a PCB, and instructions with a schematic diagram, for the incredibly low price of a few dollars. I immediately purchased one and decided to build and test it.
First, let's see what the kit consists of.
- STC15F104W single chip microcontroller
- tps70933 Voltage regulator wich provide 3.3V for microcontroller
- TC4427 Dual High-Speed Power MOSFET Driver - Which directly drives the ultrasonic transducers
- Two ultrasonic transducers
- 3 PCBs
- Bumpers with screws
- Schematic diagram
- And a few passive SMD components, resistors and capacitors

This project is sponsored by Altium 365 . Altium 365 is a cloud-based platform designed for electronics design and engineering. It provides a suite of tools for PCB design tools, including Requipments management, Supply chain, Library managment, ECAD connectivity, Co-design and integration, and manufacturing portal.

It is immediately clear that these are very small SMD components, so soldering with a standard soldering iron will be a real challenge and exercise. I was really positively surprised by the use of a microcontroller in this inexpensive device, so I hope it will work well. Now I will approach soldering the components using a magnifying glass with high magnification, keeping in mind that well-soldered components are a basic requirement for the proper functioning of the device. I will skip this part so as not to overload the video and devote more time to testing.

After soldering the components, I visually inspected the PCB and checked for any errors or short circuits. Then I connected the device to a laboratory power supply for the first time with the current protection activated at 150mA. As you can see, the constant current protection is activated, and the TC4427 chip heats up, which is an almost certain sign that it is not working.

Fortunately, I had a UCC27524 IC from one of my previous projects for making a Tesla Coil. This chip has an identical pinout as the TC4427, only it is designed for much higher currents. So it can be put in its place without any modifications.
Let me explain the basic principle of operation of this device. When both transducers are activated, they emit ultrasonic waves toward each other. The waves interfere with each other, creating a standing wave pattern in the space between the transducers. In a standing wave, there are fixed points of maximum displacement (antinodes) and points of no displacement (nodes). The nodes are regions of low pressure, while the antinodes are regions of high pressure. Small lightweight objects placed in the standing wave experience an acoustic radiation force. This force pushes the objects toward the nodes (low-pressure regions) of the standing wave, where they become trapped, and they float.

To form standing waves, it is necessary to place the two transducers at a precisely defined distance, which roughly represents an integer multiple of half the wavelength. Specifically in our case, for a frequency of 40 kHz the half-wavelength is 4.29 mm, which means that the distance between the transducers can be n multiplied by 4.29 = 4.29mm, 8.58mm, 12.87mm, etc... This distance may vary slightly depending on atmospheric conditions.
Now, let's perform some basic tests and see if and how the device works in real conditions. First, with this small oscilloscope I want to look at the shape and frequency of the signal that is generated by the microcontroller and then amplified by the mosfet driver chip.

We measure this signal directly at the transducer. So we can see that a clean rectangular signal with a frequency of 40 kHz is generated. This is a good sign for normal operation of the device. Taking into account the previous calculations, the distance between the transducers is about 2.5 cm. Next, we need to carefully try to place a small Styrofoam ball in the space between the two transducers. In this part we need to be patient, because we will need more time to practice placing the particles. We may also need to experiment a little with the distance.

And finally, a brief conclusion. This is an incredibly cheap and visually fascinating toy through which we can learn a lot about the behavior and physics of standing waves, and also a great way to practice soldering SMD components.
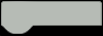